In the early stages of our manufacturing career, it was relatively rare that we would have contact with the end user of our products. Traditional routes to market mean that for most Glulam manufacturers, the glulam member is supplied to a wholesaler who in turn sells the beam to a merchant who then supplies a builder who had procured the beam for their client – the end user, perhaps an excited couple building their dream home with rich, lustrous exposed Tasmanian Oak rafters.
Given this route to market, the kind of feedback that would invariably flow to us regarding our beams would predominantly revolve around supply times, the way the beam was wrapped or whether our beams were .50c more or less expensive than the price of another supplier. Attempts to ask our merchant contact ‘how the beams went on site’, or whether the client had appreciated the extra sanding effort given what we understood about the application would often be met with “no news is good news mate” which after a while becomes strangely unsatisfying!
It is only in recent years with the advent of social media etc. that we have had the pleasure of increased contact with the end client or architect which makes for a very different style of feedback in relation to our product.
I remember years before social media afforded us this regular contact, receiving a phone call late one afternoon in the office. The caller demanded whether I was “such and such who had provided a beam through so and so four weeks ago”. Eventually, I was able to determine that yes indeed I was the manufacturer of large hardwood Glulam ridge beam that had been supplied through a local merchant and recently installed in this gentleman’s home. “Well… I’m sitting in my lounge staring up and looking at it” I braced myself not knowing what was coming next. “It’s beautiful”.
A sigh of relief. In rapturous tones he proceeded to regale me with the features of his beam and concluded by asking me to pass on his sincere thanks to the team. It was great for our team to receive this kind of response and was a powerful reminder of the existence of the ‘often invisible’ customer at the very end of the line.
In this case, the customer had ordered an ‘A Grade appearance’ beam which had been prepared with the expectation that it would be an exposed feature in the house.
There are three main ‘appearance grades’ used in the Glulam industry as defined by the current Glulam standard AS1328.2 1998. It is important to note that appearance grades relate only to the aesthetic appearance of the visible surfaces of beams and have no relationship to structural performance.
“It was great for our team to receive this kind of response and was a powerful reminder of the existence of the ‘often invisible’ customer at the very end of the line”
A Grade beams
A grade beams are ‘intended for use in applications where appearance of the member is important and clear or painted finishes are used. All surface voids are filled or repaired. Unless other use is specified, the surfaces shall be sanded to a minimum of 60 grit finish’. There is a tolerance in A grade for knot holes of a circular diameter under 30mm and other specific measures for ‘elongated’ holes and ‘edge checks’.
B Grade beams
‘B Grade’ Glulam beams are described as follows: ‘this grade is intended for use in painted applications where surface appearance is important, but a machine planed finish is acceptable. Occasional skips in the surface are permissible and minor blemishes, voids and manufacturing want shall be acceptable. The outermost laminations shall be free of loose knots and voids’. The majority of Glulam beams are produced to this aesthetic grade. Many beams with a B Grade aesthetic can be installed ‘as is’ and painted. Generally however, a B grade beam differs from an A Grade beam in that it will not have been fully sanded. A little ‘elbow grease’ on site may be required to deal with the ‘occasional skips’ or ‘minor blemishes’ with the ultimate result to be worked out between the builder, painter and client.
C Grade beams
C Grade beams are defined as ‘intended for use in applications where surface appearance is not important. All blemishes and voids are acceptable’. Structurally these beams should be as strong as any other beam, but they will be ugly. This is the Picnic Bar of Glulam and increasingly a rare beast! Glue runs, gaping knots, wane and even bark may find its way onto the inner laminates of these beams. They are generally structural members inside roof cavities or behind walls. Less and less manufacturers offer a genuine C grade beams since Glulam manufacturing technology has made it increasingly difficult to produce a beam this ugly even if one tries! There’s also been too many cases of builders choosing the ‘C Grade’ option to “save costs and sand it myself” only to find that the difference between a C Grade beam and a B Grade beam is very real indeed.
Knot not wanted
Glulam manufacturers may choose to provide a custom finish at the specific request of a client. One we’ve heard a few times is “no knots at all please”. The first time we received this request, our response was to recommend to the prospective customer that perhaps ‘plastic’ might better suit their requirements! Having established however, that timber remained the product of choice a docking and grading program was designed, a suitable price negotiated, and beams produced to the customer’s satisfaction. Conversely, Glulam manufacturers have also had requests for ‘feature rich’ beams with ‘warts and all’ desired for aesthetic effect.
One more anecdote involving Glulam appearance grades involves a time back in the day when Oregon Glulam beams were still in vogue. One builder we supplied through a local merchant had several beams in each build – large members approximately 400-500 x 130mm in lengths from 7.2 to 12.0m long. The merchant order always specified that these beams be made to an ‘Appearance Grade A’ and as the manufacturer we always dutifully complied and invoiced accordingly! Years of supplying these beams went by with nary a complaint and it was always a pleasure to inspect the finished product on the stools prior to these beams being wrapped. One day the builder rang and apologising for the direct contact, proceeded to explain that the latest batch of beams were needed more urgently than usual. The merchant had provided our contact details so that the builder could apply lead time pressure directly to the source. I endeavoured to tactfully explain that although the beams had been made we were still in the process of ensuring the A Grade finish which meant at least one more day of work on the beams. The builder expressed surprise and proceeded to explain that every one of the Oregon beams he used went straight into the roof and were completely covered – never to be seen. The beams were subsequently delivered ‘as is’ and I do believe the merchant instructed to order B grade beams thereafter and “pass on the savings please”! I thought of the many thousands of dollars in premium pricing paid over the years for A grade beams used in a C grade application. Somewhere, blissfully unaware home occupants live under plaster ceilings, above which sits some of the most beautiful Oregon beams we ever produced! We still appreciate them even if they can’t!
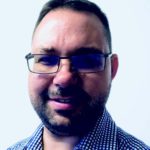